西门子编码器短路故障维修早知道:西门子编码器作为工业自动化控制系统的核心组件,其稳定运行对设备精度至关重要。我们凌坤自动化有着丰富的西门子编码器维修经验,如果遇到困难无法解决的问题欢迎来电咨询。
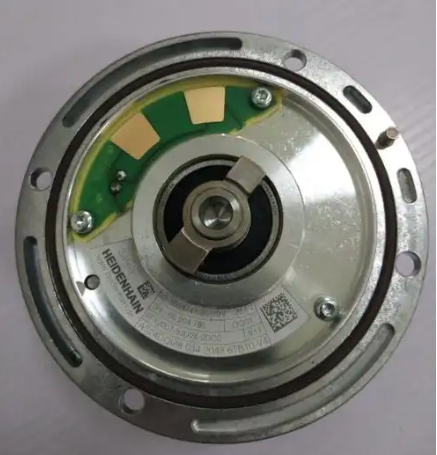
西门子编码器短路故障的主要原因
西门子编码器短路故障可能由多种因素引起,准确识别根本原因是高效维修的第一步。根据工业维修实践,这些故障通常可归纳为六大类,每种类型都有其独特的症状和解决方案。
编码器内部元件故障是较为常见的短路原因之一。长期运行在恶劣环境中,编码器内部的精密电子元件如电阻、电容和晶体管可能因老化、电压冲击或质量问题而损坏。
连接电缆问题在实际故障中占比很高,主要包括电缆断路、短路以及接触不良三种情况。编码器电缆长期受到机械运动带来的弯折、拉扯,或环境中的油污、化学物质侵蚀,都可能导致绝缘层破损引发短路。连接器部位因振动造成的松动,以及接头氧化导致的接触电阻增大,也是信号异常的常见诱因。
电源系统异常对编码器工作稳定性影响重大。西门子编码器通常需要稳定的+5V供电(允许范围一般为4.75V-5.25V),若电源电压因配电系统问题而波动或跌落,会导致编码器工作异常甚至损坏23。电源问题可能源于电源模块故障、线路压降过大或与其他大功率设备共用电网导致的干扰。
机械安装问题虽然看似简单,但却是许多隐性故障的根源。编码器安装松动会导致轴对中不良,引起机械振动和信号抖动;安装底座刚性不足会产生谐振,影响信号稳定性;轴连接过紧则会增加轴承负荷,加速磨损。
其他特殊故障包括编码器内置电池电压降低(导致绝对值编码器数据丢失)、轴承磨损引起的机械振动、以及光栅/磁栅污染导致的信号衰减等。
西门子编码器短路故障的专业维修方法
确定编码器短路的具体原因后,需要采取针对性的维修措施。不同故障类型的维修方法和复杂程度差异很大,从简单的电缆更换到精密的编码器内部元件修复,维修人员应根据自身技术能力和设备条件选择合适的维修策略。
电缆系统的修复与更换是处理连接故障的主要方法。当检测到电缆断路、短路或绝缘不良时,最彻底的解决方案是更换整根电缆。选择替换电缆时,必须确保其规格(线径、屏蔽类型、阻抗特性)与原装电缆一致,特别是对于高速编码器信号,电缆参数不匹配会导致信号完整性问题。更换电缆时,注意正确接线,通常编码器电缆包含电源线(+5V和GND)、信号线(A、A-、B、B-、Z、Z-等)和屏蔽层,必须按照引脚定义一一对应连接。对于局部损伤的电缆,在紧急情况下可进行局部修复,如剪断损伤段后重新连接,但需注意接头处的绝缘和抗干扰处理,这种方法只适用于临时应急,长期使用仍建议更换整根电缆。
电源系统的修复对保证编码器稳定工作至关重要。若检测到电源电压不稳定或不足,首先应检查电源模块的输出是否正常。对于开关电源,检查滤波电容是否老化,电压反馈回路是否正常;对于线性电源,检查调整管和散热条件。若电源本身正常但编码器端电压不足,可能是线路阻抗过大,此时应缩短供电距离或加大线径(建议使用截面积不小于0.5mm²的铜线)。在干扰严重的环境中,可在编码器电源端增加LC滤波电路,使用10-100μF的电解电容并联0.1μF的陶瓷电容,能有效抑制高频干扰。对于特别敏感的绝对值编码器,建议使用隔离型DC/DC电源模块,避免地回路干扰。
编码器内部维修可尝试拆解编码器进行检查。拆解时需注意防静电措施,使用接地腕带并在防静电垫上操作。常见可修复的内部故障包括:电源滤波电容短路(更换同规格电容)、信号输出芯片损坏(查找替代型号更换)、光耦器件老化(更换同型号光耦)等。对于光电编码器,光栅盘污染可用无水酒精轻轻擦拭;对于磁编码器,磁栅污染可用无尘布清洁。编码器轴承磨损会导致轴晃动影响信号精度,需使用专用工具更换同型号轴承。维修后重新组装时,必须确保各部件位置精确,特别是光栅盘或磁栅与传感器的相对位置。
屏蔽系统的完善对解决干扰相关问题效果显著。编码器信号易受电磁干扰影响,特别是与变频器、伺服驱动器共用安装环境时。确保使用双层屏蔽电缆(内层铝箔屏蔽+外层铜网屏蔽),外层屏蔽层在驱动器端单点接地(通常通过连接器金属壳接地),内层屏蔽可在编码器端接地。避免屏蔽层作为信号回流路径使用。对于特别恶劣的电磁环境,可使用金属导管或屏蔽槽走线,并将导管良好接地。检查编码器外壳接地是否良好,接地线应短而粗,连接点无油漆或氧化层。信号线采用双绞结构能有效抑制低频干扰,特别是对于长距离传输的差分信号(如A-、B-、Z-)。
机械安装的校正能解决许多与振动、偏心相关的问题。重新安装编码器时,确保轴对中精度(径向偏差<0.05mm,角度偏差<0.1°)。使用柔性联轴器补偿微小偏差,避免刚性连接带来的应力。编码器安装底座应有足够刚度,避免共振放大。固定螺丝应按照对角线顺序逐步拧紧,确保受力均匀。对于高转速应用(>3000rpm),建议进行动平衡校正。安装后手动旋转轴体,应感觉平滑无卡涩,无异常摩擦声。机械安装的精确校正不仅能解决当前故障,还能延长编码器使用寿命。
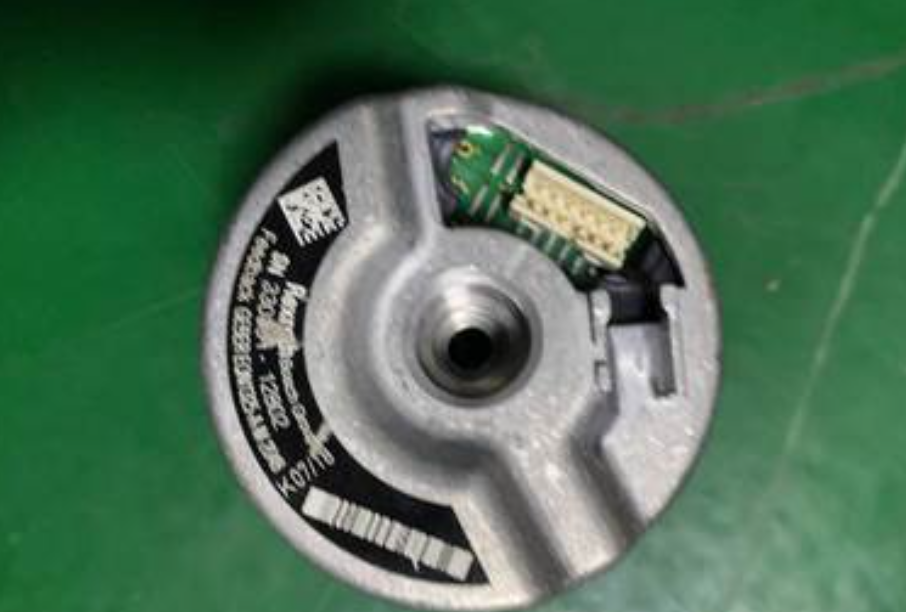
维修后的测试验证是确保维修质量的关键环节。维修完成后,应先进行静态测试:测量各线路电阻、绝缘电阻,检查电源电压79。然后进行动态测试:低速旋转编码器,观察信号波形是否正常;逐步提高转速,检查信号稳定性,特别是高转速下的波形质量。对于绝对值编码器,还需检查位置数据的连续性和正确性。最后在实际设备上进行联机测试,运行典型工作程序,验证全工况下的可靠性。完整的测试流程能发现潜在问题,避免二次维修。